Kaizen Training and Philosophy
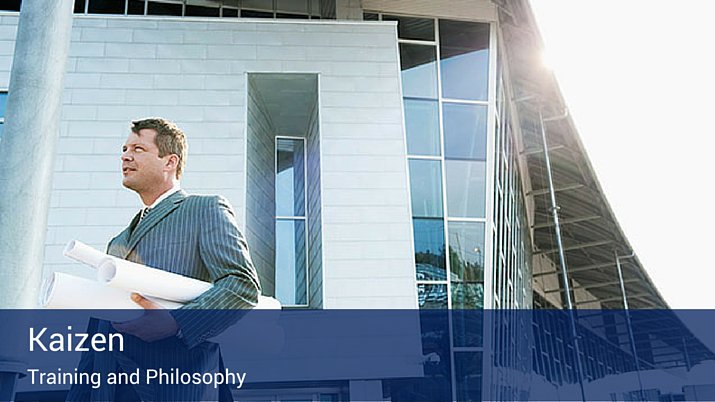
Last Updated October 19, 2023
Developed in Japan after World War II, Kaizen business philosophy involves promoting constant improvement by monitoring business processes and making ongoing adjustments. The term is taken from two Japanese words that literally mean “good change.” Built on the Deming Cycle (plan, do, check/study and act), Kaizen philosophy can permeate all aspect of business culture in an organization committed to promoting its methods.
Streamlining and simplifying business processes can increase profit potential and improve workplace harmony.
This Kaizen approach includes:
- Standardizing operational processes and other organizational activities
- Defining meaningful and relevant measurements of looking at operation cycles
- Gauging performance against requirements
- Innovating new requirements, procedures and methods to increase productivity
- Standardizing change and monitoring impacts
- Continuing the cycle ad infinitum
For project managers and other leaders looking for ways to influence change from the top down and bottom up, organizational Kaizen training could be considered.
While many of the ideas are understood throughout business as best practice approaches toward business problem-solving, formal Kaizen training provides an opportunity to jump start a synergistic integrity within an organization. In addition, team training can clarify organizational goals and provide an on-going dynamic forum for sustained momentum toward increased effectiveness, efficiency and profitability.
Because this philosophy supports personal responsibility for organizational growth, employees at any level are encouraged to contribute to the conversation regarding perpetual change and improvement through their team leaders. No matter who comes up with a suggestion for improvement, the Kaizen philosophy indicates that the suggestions should be equally considered. In many U.S. businesses, a comment or suggestion box is a common interpretation of this idea.
Wasteful Areas According to Kaizen
While Kaizen is meant to help all parts of an organization, there are seven areas which tend to accumulate the most waste. As a result, these areas are of particular importance.
- Over-production
- Delay times (waiting)
- Excess inventory
- Transportation
- Over-processing
- Motion (redundant or unnecessary processes)
- Defective Units
Working with division leaders, Kaizen-trained professionals implement change that can lead to more effective processes, a more harmonious work environment and a more profitable and reliable product or service.
In addition to directly impacting a workplace, training offers other important benefits. Through national and international networking, Kaizen professionals can benefit from increased opportunities for career growth, as trained leaders are highly marketable in today’s competitive economy. By attending conferences and being active in online and regional communities, professionals have the opportunity to continue career growth and leadership development.
Implementing Kaizen Methods Impact
Organizations as diverse as T-mobile and Goodwill Industries have implemented Kaizen methods to support Lean business practices in recent years. T-Mobile used Kaizen methods to train 100 employees who then worked throughout the organization to:
- Improve down-time response time
- Improve overall productivity by 25%
- Implement system upgrades without increasing workforce, despite significant downtime due to extreme weather events
Ultimately, T-Mobile effectively used Kaizen methodology to mitigate a business challenge which was completed on time and within budget.
In the case of Goodwill Industries, a particular Oregon location sought to increase its effectiveness and efficiency with stock processing and other organization challenges. As a result of training and staff development, the use of Kaizen methods resulted in doubling the location’s staff size, increasing profitability and processing a greater amount of merchandise on a weekly basis. In this particular case, Kaizen directly empowered the management team to positively impact the lives of dozens of disabled and developmentally challenged individuals by increasing their employment opportunities within the local community.
As these examples demonstrate, Kaizen training can not only help improve business, but can transform lives of people within an organization or community.