Ways to Avoid a Six Sigma Project Failure
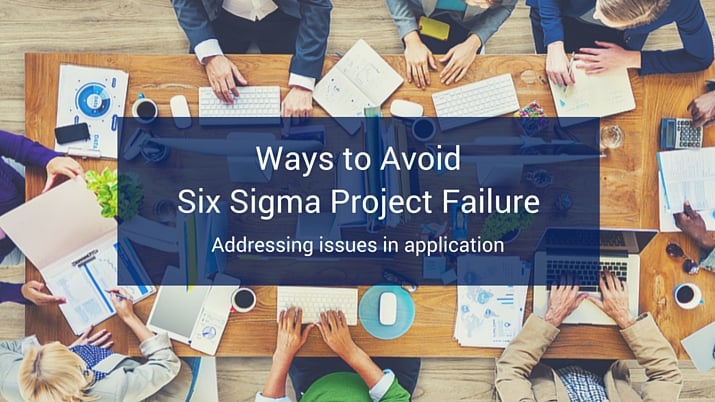
Last Updated March 8, 2024
What happens when a process improvement method fails to improve a failing process? Experts are finding that in some organizations, between 60% and 80% of these projects are failing to deliver the improvements they promise.
This forces the question: Is it the methodology itself, or is the problem in the application?
Six Sigma deploys the DMAIC cycle to methodically find and eliminate process defects. It uses objective statistical tools to precisely identify process defects and recruits A-level employees with expertise in both Six Sigma and the process in question.
With factors like these working in its favor, why aren’t some organizations getting better process improvement results from Six Sigma?
Six Sigma enthusiasts are quick to point out that a project doesn’t fail because Six Sigma principles and statistical tools don’t work. Projects tend to fail because of how teams apply the Six Sigma methodology. This flawed application can take on several forms:
- Little or no support from upper management – Regardless of how accurately a project team can identify a flaw in a production process, or how elegant their solution to the problem is, without the support and involvement of the organization’s leadership, the solution is not likely to become part of daily operations. Projects need the support of leadership to obtain financing, overcome obstacles and to help the team’s improvements take root in company culture and become a permanent part of doing business.
- Erratic team leadership – Project teams are usually captained by an experienced Black Belt who keeps the team on track and moving forward. However, once the team starts making progress, the Black Belt is usually transferred to another project. Once a project team loses strong leadership, it risks losing sight of its objective and not meeting its performance goal.
- No connection to financial performance – Let’s face it – in business, money talks. Six Sigma initiatives that have a tie to decreasing costs or increasing revenues gain more attention, command more respect and get more support than projects not directly connected to financial performance.
How to Improve Quality Improvement Projects
Several actions can address common reasons for Six Sigma project failure:
- Bridge the gap with management – Management support and involvement greatly increase a project’s chances for success. When top leadership puts its full support behind a Six Sigma project, it typically encounters much less resistance. Public declarations of support are important, and management’s direct involvement in Six Sigma initiatives through Black Belts and Master Black Belts are also crucial for success.
- Consistent team leadership – If possible, keep the Black Belts who lead Six Sigma teams in place until the project is completed. If a long-term commitment is not possible, make sure Black Belts have groomed a successor to replace their leadership on the team. Where feasible, keep Black Belts assigned to the team as part-time leaders.
- Promote a project’s financial impact – Make sure that a project’s benefits can be expressed in terms of dollars saved or revenues increased. A project with easily-understood financial benefits helps focus the attention of both its team members and the organization’s leadership.
Using Six Sigma principles does not guarantee successful process improvement. The key to success is in applying Six Sigma methodology strategically and correctly. Correcting the problems that are most common in Six Sigma projects can help increase your odds of successful process improvement.